GRC It refers to glass fiber reinforced cement, which means "alkali resistant glass fiber is used as reinforcement material, low alkalinity high-strength cement mortar is used as cementation material, and light inorganic composite material is used as aggregate.
"GRC has thin components, high flexibility resistance, good impact resistance, low alkalinity, small free expansion rate, reliable crack resistance, stable quality, moisture-proof, heat preservation, incombustible, sound insulation, sawable, drillable, nailable, planable, chiselable, simple construction of wall surface, avoiding wet work, improving the construction environment, saving land resources, light weight and reducing load in buildings, (1/6-1/8 weight of clay brick) Reduce the foundation, beam and column reinforced concrete, reduce the total project cost, and expand the use area.
Because CRC is light Partition board It is installed in the non bearing parts of the building, and the required installation parts are all places with large span settlement deformation and weak load resistance. Because the light partition board groove is the particularity of assembly connection and smooth surface, it is easy to cause cracks at the connection between plates, and between plates and doors and windows. When concentrated load is applied, it will cause vibration deformation of the light partition board, The occurrence of cracks and hollowing puts forward new topics and some prevention measures for the assembly method of GRC battens, pipeline embedment, opening, grooving, appliance installation, surface plastering quality problems, etc.
below, Baotou GRC For the crack problem, after a lot of research, the following measures are usually taken:
1. Improve the production and installation process of GRC board to prevent cracking of board joints
1.1 Since the traditional plate making process uses socket connection (Figure 1), workers generally apply sand plaster in the groove before splicing and extruding during installation. In this way, it is difficult to ensure that the mortar at the joints is full. Instead, the butt joint connection (Figure 2) is used. After the sand mortar is plastered on both grooves, the butt joint will extrude the mortar to ensure the fullness of the mortar.
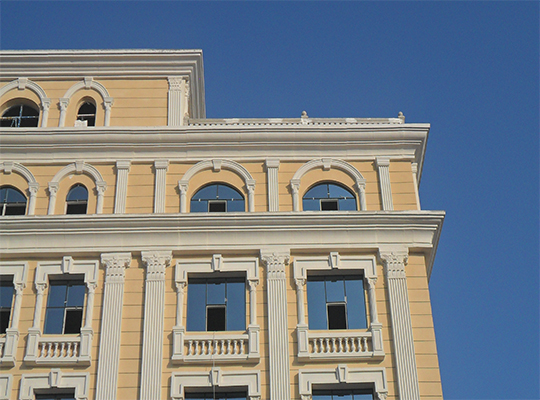
1.2 10 days after the installation of partition board, check whether all gaps are well bonded and whether there are cracks. If there are cracks, find out the causes and repair them. All board joints and internal corner joints that have been well bonded shall first be cleaned of floating ash, scraped with adhesive, pasted with 100 mm wide glass fiber mesh cloth, and the corner partition wall shall be pasted with a layer of 200 mm (100 mm wide on each side) glass fiber cloth at the external corner, compacted and bonded, and the surface shall be scraped with adhesive.
1.3 Glass fiber tape and glass fiber cloth: the cloth weight is more than 80 g/m2; Breaking strength: 25mm × 100 mm strip: warp yarn is greater than 300N; Weft yarn is greater than 150N.
2. Strengthen the curing of joint mortar
After the installation of GRC board, the joint mortar shall be cured in time, and the curing time shall not be less than 7 days.
3. All temporarily fixed wooden wedges must be removed
In the standard practice of installing wooden wedges for temporary fixation between plates, beams and columns, the wooden wedges soaked in asphalt paint can not be removed. However, during immersion, the asphalt paint used is often not saturated or unqualified, which cannot meet the requirements of waterproof and anti-corrosion. When making the ground, the wooden wedge will absorb water and expand. After drying and shrinking, it will cause deformation and cracks in the GRC board. Therefore, the wooden wedge used for temporary fixation needs to be completely removed after it is filled with mortar or fine aggregate concrete and has relative strength.
4. Reinforcement of door and window openings
At the junction of the door head plate and the wall, in addition to fixing with U-shaped steel plate clamps, the bottom is fixed with L-shaped angle steel clamps, and 200 mm is paved along the door and window openings × 300 mm reinforcing mesh, forming a 45 ° angle with the opening (Figure 3).
5. Avoid cracks on GRC board
In plate distribution, not only the rationality of wall plate combination shall be considered to avoid the occurrence of less than 2/3 plates, but also the reserved hole positions of water, electricity and other disciplines shall be marked in the plate distribution drawing at the same time. It is required that small holes should be completed before installation to reduce the vibration caused by opening after installation. When it cannot be completed before installation, the opening can be carried out only after the strength of the joint mortar reaches 100% (28 d), and the cutting machine is required to open the hole.
6. Curing age of GRC board
Ensure that the GRC board age should not be less than 28 days, and should not be less than 14 days of aging. Many smaller manufacturers carry out scale measurement when receiving engineering tasks. Due to the tight construction period, GRC boards were transported to the construction site for installation before reaching the kettle time, and the curing age was seriously insufficient.
7. Polymer mortar is used for joints
Since the shrinkage of cement determines the self shrinkage cracks of ordinary mortar during solidification, polymer mortar shall be used for joints to alleviate the cracks caused by mortar shrinkage.
8. Brush 801 glue on the surface of GRC board and nail steel wire mesh
In the production process of GRC board, the manufacturer mostly uses release agent in order to make GRC easy to release. A layer of 801 glue slurry with a thickness of 2-3 mm shall be evenly painted on the cleaned GRC wall board, and steel wire mesh shall be fully nailed on the surface of the GRC board. Nailing machine shall be used to nail into the plate body along the vertical and horizontal direction for connection, and the spacing shall be 250mm in both directions. The top and both sides of the batten are connected to the concrete column and wall, and then L-shaped additional steel wire mesh is used for pasting to enhance the connection strength.
9. Improve the mortar mix ratio
Take two different mix proportion schemes, make 10m2 samples respectively, and observe after one month. It is found that no crack is found in Scheme II, either in the plate or at the internal corner (Table).
10. After finishing the decorative surface course, it shall be properly watered for curing
The construction of the decorative surface of most projects is in spring and summer. With high ambient temperature and strong wind, it is easy to cause air cracks on the surface layer or hollowing cracks due to too fast drying. Generally, water spraying curing shall be carried out twice a day for at least 3 days to make the surface strength meet the design requirements. The above construction methods have been successively practiced in the project, installing GRC boards and carrying out decoration layer construction of more than 20000 m2. Some projects have been completed for 4 years, and no cracks have been found so far.
@Disclaimer: The reprinted content is from the network. If you have any objection, please contact me in time, and I will delete it.