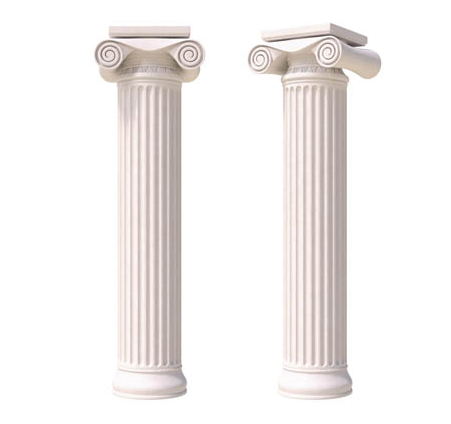
The mould shall be made in strict accordance with the drawing size and specification. In terms of installation and production, full consideration should be given to mold separation, and reserved bolt sinking position and welding spot. finished product GRC The product demoulding must be considered for the component mold, and the mold shall not be stuck. The drilling hole at the sunk bolt position must be vertical, and the deformed mold cannot be put into production.
Batch: It is composed of components with the same raw materials, the same process and the same specifications. Each batch of 500 pieces, if less than 500 pieces, is also regarded as a batch.
General judgment: under the condition that GRC type inspection is qualified, when the production quality, appearance quality, size deviation and bending ultimate strength meet the requirements of the corresponding level of the standard, this batch of members is judged to be members of the corresponding level.
Stressing bag: thicken the GRC counterbolt hole by 2~2.5cm, but at least 1cm lower than the installation surface, with a diameter of 3~5cm. At the same time, lay a small piece of glass fiber mesh cloth.
Rolling: extruding GRC shall be trimmed evenly, and the edge must be flush with the mold boundary and end plate. For products to be welded, reserve welding spots. Reduce the content of chloride ion in GRC components. The chloride ion content has a great impact on the corrosion of reinforcement. Excessive chloride ion will damage the passive film on the surface of reinforcement, resulting in corrosion of GRC component reinforcement. In GRC material control, it is strictly prohibited to use sea sand, regularly detect the chloride ion content in the sand, and it is strictly prohibited to use industrial waste water with excessive chloride ion content to mix mortar.
*Disclaimer: The reprinted content is from the network. If you have any objection, please contact me in time, and I will delete it.