Baotou GRC The lightweight components are mainly made of alkali resistant glass fiber as reinforcement material and sulphoaluminate low alkalinity cement as cementation material, and are mixed with suitable aggregates through production processes such as spraying, formwork erection pouring, extrusion, grouting, etc. Early mainly used for GRC Lightweight hollow Partition board GRC composite exterior wall panel, GRC grid panel, GRC light slab. With the development of production technology and the improvement of equipment, GRC decorative products began to appear at the end of the 1990s and began to be widely used in recent years. This paper analyzes many factors that lead to the cracking of GRC light components, briefly introduces its countermeasures and solutions, and puts forward suggestions for the use of GRC in combination with engineering examples.
1. Background
There are many facades in the first phase of a community project, and some cracks appear after a period of use, which has a certain negative impact on the facades and residents' psychology. In recent years, the extensive application of GRC lightweight components is a problem. The industry does not know enough about this problem, and cracks are very common. The Department makes a preliminary analysis of this problem by referring to some good opinions of GRC industry and its own design experience.
2. Analyze the cause of cracking.
The degree of cracking varies from region to region. The climate in the south, especially in coastal areas, is humid, and the relative humidity of air is about 90% for most of the year. In this hot and humid climate environment, the water content of GRC lightweight components is always high. If no special drying measures are taken, the moisture content of components in natural state shall not be less than 10% specified in the standard. Therefore, cracking is more likely in the south, especially in coastal areas. Cracking usually occurs at joints between members and between members and beams. The crack width is related to the dry shrinkage, cold shrinkage and transverse length of the member. Most cracks are within 0.5mm wide.
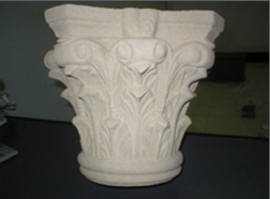
3. The current method to solve the cracking of GRC light components.
There are two main objectives to improve the material properties of components: one is to reduce the shrinkage value of components, including dry shrinkage value and cold shrinkage value, to reduce the shrinkage deformation of components; The second is to improve the elasticity of components and joint materials and increase the tensile deformation value. Through this increase and decrease, the balance between the shrinkage deformation and tensile deformation of the component is achieved as far as possible. However, the current characteristics of GRC lightweight components make it difficult to balance the tensile and shrinkage values.
In the installation structure of components, the current main direction is generally on the joint treatment and joint materials of components.
On the premise that the quality of the component itself is qualified, the joint of the component is a weak link, where cracks are easy to occur. It is difficult to prevent cracks by simply using bonding method, even if glass fiber cloth is pasted at the joints of components. The component will shrink, and it is difficult to pull it by brute force. Therefore, due to the balance between shrinkage deformation and tensile deformation, members often crack or crack. What's more, the components need to be aligned up and down during installation, and it is difficult to make the mortar full due to repeated staggered movement. Most of them are supplemented with mortar after installation, which is not easy to bond.
The method to increase the tensile deformation value of elastic mortar is correct, just to prevent cracking of component joints. However, in practice, there is a contradiction that is difficult to solve, that is, the contradiction between the high elasticity of elastic mortar and the low elasticity of component finishing materials. The tensile ratio of component facing materials (such as putty) is far less than that of elastic mortar, and the component surface will still crack. If the finish material is required to reach the same high tensile rate, the cost is unrealistic.
*Disclaimer: The reprinted content is from the network. If you have any objection, please contact me in time, and I will delete it.